Martin reliability provides full wraparound production at Engelhardt
Posted: August 06, 2010
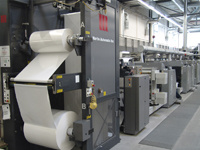
The Martin ECPF automated unwind/splicer is designed to handle filmic substrates used on the VSOP line
Engelhardt-Etikett GmbH, one of Europe's largest converters of wet glue labels with a raft of multi colour sheet fed presses at its two production facilities in Nördlingen, southern Germany, is now reporting full capacity on its Drent Goebel VSOP mid web press. The company, which is part of the Sofinim Group, diversified into the production of wraparound labels, produced on 38-micron OPP, back in 2006 from what previously had been a printing house predominantly kitted out with Heidelberg Speedmaster presses.
Explaining the change of course, Engelhardt's Production Director, Christian Martsch said: "We pride ourselves on being a single source supplier to our customers, many of which are leading international brands in the soft drinks market. For example, we had several customers that were looking to place substantial orders for wraparound labels because they saw it as a growth area. We responded by investing in the new technology."
After selective research of the market, the decision was made to stay with offset printing and to specify the widest web width available, which at that time was 850 mm, offered by Drent Goebel. The VSOP line installed is an 8-colour press with inline flexo varnishing unit, capable of running at 260 m/min. To cope with this high production capability, Engelhardt specified Martin Automatic unwind and rewind technology.
Josef Stelzle, Technical Manager at the company explained: "We preferred to follow the offset route because it was a technique we knew well. It's flexible and offers a fast time-to-market, as well as being cheaper than flexo in the critical pre-press area." In addition to altering the company's mindset from sheet to roll fed, the VSOP also required the production staff to cope with UV inks for the first time - neither an easy nor quick change to accommodate.
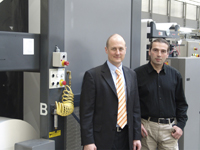
Production Director Christian Martsch (left) and Technical Manager Josef Stelzle rate the reliability of their Martin equipment very highly
Rather than recruit experienced web press operators from outside the company, Engelhardt advertised internally for applicants to form the new VSOP team. According to Martsch, it was a great success, with high levels of motivation and plenty of offset knowhow being applied to the new press. Full commissioning to commercial production was phased over a twelve-month period, largely as a result of Engelhardt's exacting quality standards, since which time the VSOP has worked triple shifts six days per week, and is up to capacity, according to Stelzle.
With the VSOP's healthy appetite for print, the two Martin Automatic units specified needed to be big and strong. An ECPF (F for Film) unwind and high-speed splicer, and an RMAP rewinder were chosen to cope with the 850 mm web width and the weight of the 1.25 m diameter rolls. These two units have ample spare capacity to cope with non-stop running, and by way of complimenting Martin on the performance of its units, Stelzle stated: "The Martin machines haven't cost us one minute of production time because they have never broken down in the entire time we have had them. We take their reliability for granted, and tend to forget they are there!"
Quizzed on the direction of the company's next investment, Christian Martsch qualified his answer by saying: "We are up to capacity on the VSOP with current work so one obvious route would be to install another similarly equipped line - but we are still evaluating market trends and may pursue a different path, if the opportunity looks attractive."
It is difficult to fault the business logic at Engelhardt. Currently, the company converts 370 million square metres of substrate each year, which amounts to 35 billion labels. Few could argue against those numbers, and just as the VSOP was installed in response to a specific demand, Engelhardt clearly has the experience and expertise to accurately predict where its next investment should be.